
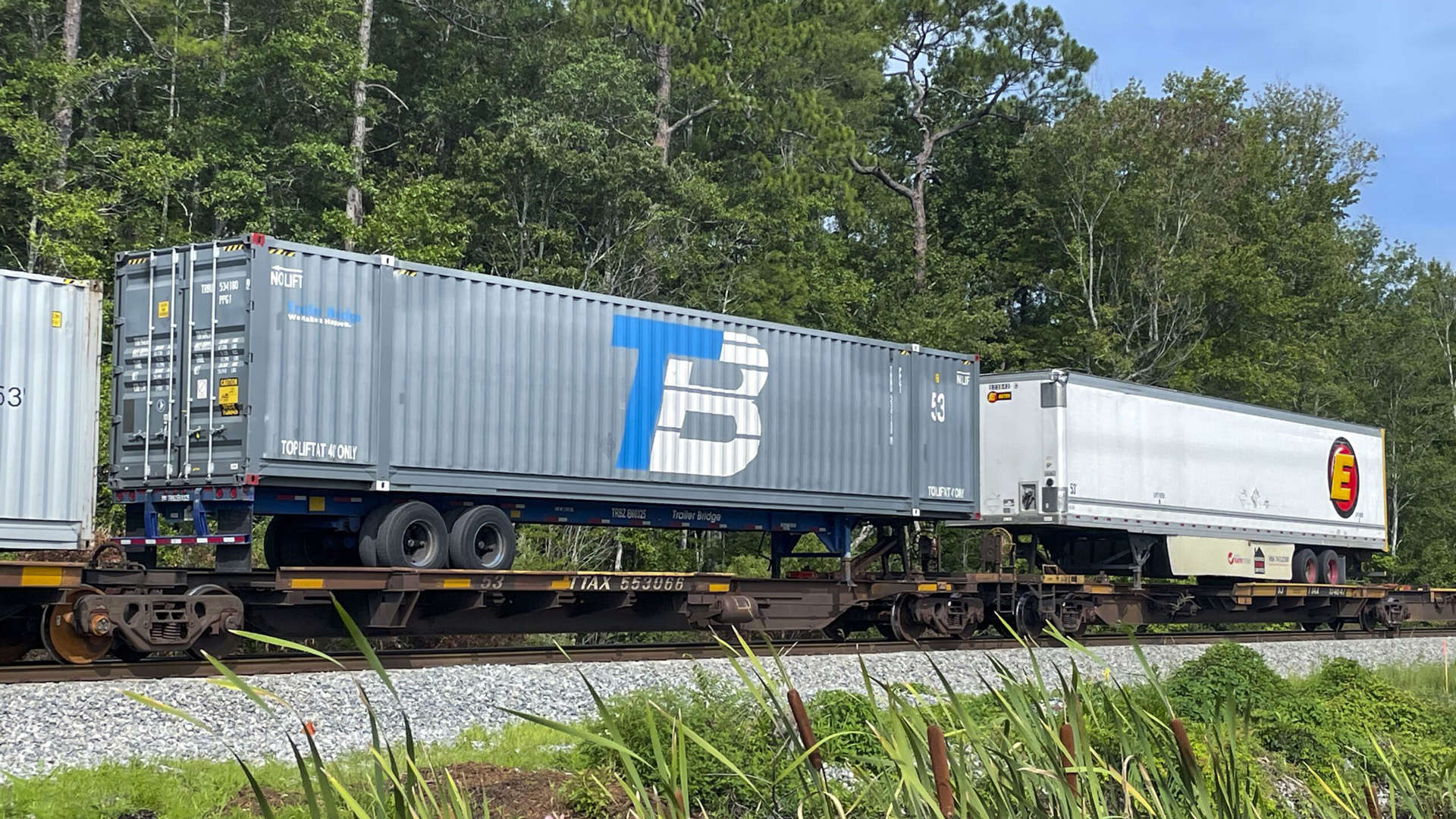
What Does the Future Hold for Intermodal Freight?
It’s no secret that the transportation industry has experienced a disruptive two years, but for intermodal and rail transportation, some say it was hit the hardest. While volumes were only down 1.8% from 2019 to 2020, intermodal struggled to regain market share. Entering 2022, the January volume had decreased 13.3% from prior year. The continual stress on the supply chain has impacted ports, rail networks, equipment capacity, drayage capacity, and warehouse issues. As the entire industry works to get itself back on track, intermodal is implementing new initiatives with a little help from fellow industry partners.
Equipment Capacity
Particularly in today’s retail market, large companies are canceling orders due to high inventory levels. Combine the full inventory with limited warehouse space to unload the product, container unload times are increasing and therefore reducing container and chassis capacity.
According to JOC.com, Railroads and intermodal equipment providers (IEPs) have ordered more than 10,000 new 53-foot chassis to arrive sometime this year which may help decongest the port terminals, but only if improvement in other logistics arenas takes place. “The inability of receivers to unload containers quickly has been a major driver of the decreased intermodal volume,” said Eric Masotti, President of Logistics at Trailer Bridge. “Ordering new equipment will definitely bring some relief, but we have to find a solution in the interim until that equipment arrives.”
Bringing in new equipment, however, is just a piece of the puzzle to get intermodal volumes on the rise again.
Labor Issues
The pandemic resulted in mass layoffs across the industry. Fast-forward to now, those employees that were initially laid off have moved on and are not returning to logistics, compounding the worker shortage. “Many workers’ priorities have changed and require more flexibility and want safety concerns addressed,” said Masotti.
The pandemic, however, is not the only thing to blame. Precision Scheduled Railroading (PSR) was implemented long before COVID-19 to boost rail efficiency. Under this practice, inefficient or low-volume lanes were eliminated resulting in layoffs across the board. While the outcome generally improved operational performance metrics, the railroad workers say it has resulted in staffing shortages, decreased wages, demanding and dangerous working conditions, and an exhausting attendance policy.
These are the key concerns and reasoning behind the two-year delay of the union worker contract agreement. While President Biden appointed a Presidential Emergency Board (PEB) to propose a compromise and aid in avoiding a worker strike, many union members feel it is only delaying the action instead of addressing it head on. As of August 30, 2022, only three of the 12 rail unions have reached tentative agreements. The nine remaining unions and carriers have until mid-September to come to an understanding or face the possibility of a labor strike.
There is no silver bullet to fix the current labor issues leaving the industry to remain patient as the unions and railroads continue to work through their contracts. In the interim, understanding how these shortages impact customers and transportation partners can help guide your company to cross-functional initiatives that can be implemented quickly and effectively.
Collaboration and Technology to Increase Efficiencies
Over the past year, both rail and trucking companies have consolidated efforts to advance efficiencies, increase capacity, and get intermodal freight moving in an upward direction. In March, J.B. Hunt and BNSF Railway announced a collaborative endeavor to improve intermodal capacity while continuing to meet the needs of current customers. Hunt’s plans to grow its intermodal fleet to approximately 150,000 containers over the next three to five years will be met with BNSF agreeing to provide increased efficiency at several of its property locations around key intermodal hubs in Southern California, Chicago, and other markets. “With domestic carriers shifting western railroads, the need to backfill lost volume remains,” stated Masotti. “Hunt and BNSF will aggressively be pursuing market share with the volume that is being transitioned to Union Pacific and J.B. Hunt’s investment in an additional 50,000 containers reflect their commitment to growth.”
UP recently rolled out its latest technology, Precision Gating Technology (PGT). This technology automates the check-in process for truck drivers, helping them get in and out of the intermodal terminals as quickly as possible. When used with UP’s mobile app, UPGo, PGT scans the driver’s equipment and automatically begins the in-gate process – allowing the driver to head directly to their assigned parking spot. Without it, entering the terminal includes checking in the container or trailer, ensuring the container is in the right location, and completing paperwork.
To determine if these newly developed partnerships and technology are working will all depend on analyzing the speed of the container throughout its journey. One area all intermodal providers see the need to strengthen is velocity. “Implementing new processes and software that can increase driver productivity and reduce wait times is a huge win for both drayage companies and shippers,” said Masotti. “It will be interesting to see where these initiatives take us a year from now.”
Moving Forward
As the intermodal market continues to make a comeback, it’s not just on the service providers to make improvements. It’s going to take all parties including the shippers and receivers working together in tandem to come up with the best solution.
Here are three areas shippers can immediately apply their focus:
1. Plan for the unexpected.
As a shipper, being well positioned to respond to rapidly changing conditions provides a great advantage to your cargo, decreasing delays and preventing potential accessorial charges in your supply chain strategy.
2. Overcommunicate.
This rings true during times of crisis or change but communication should always be at the forefront of everyday operations. Having constant communication with your providers on the regular will only benefit you in the long run – allowing your provider to serve you in the best way possible.
3. Find the best fit for your cargo.
There is no ‘one size fits all’ solution. Consider alternate transportation methods when you hit a roadblock. By doing so, the likelihood of your freight staying on schedule increases. If you are determining whether intermodal shipping is right for you or would like further insight into the market, connect with one of our intermodal experts. Through our network of rail providers and carriers, we’re here to guide you to optimal supply chain efficiencies through flexible end-to-end solutions. Contact us to get started rail@trailerbridge.com.